insights
Capacity Closures in the US Corrugated Board Market
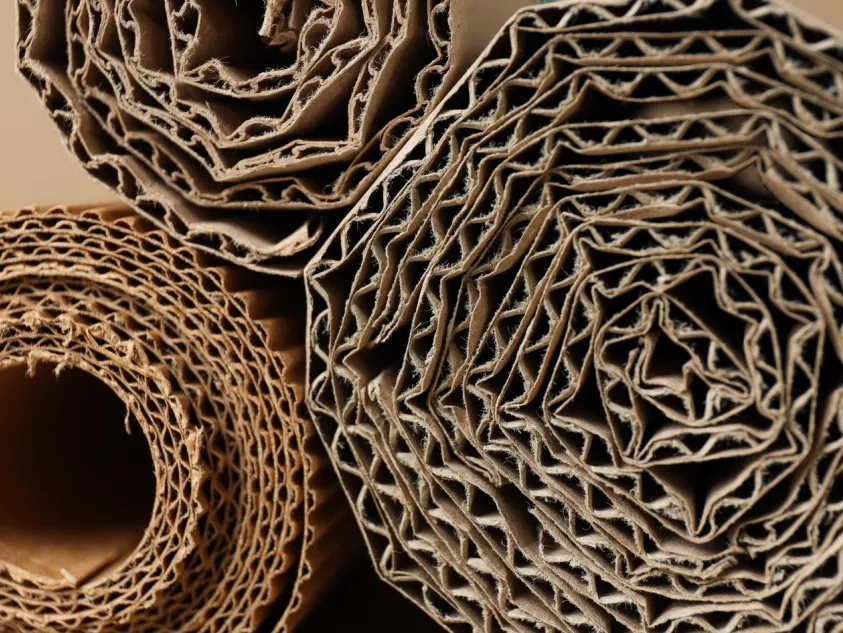
The US corrugated board industry is undergoing a historic correction marked by rapid and large-scale capacity closures totaling around 3.5-4 million tons since 2023 and around 2 million tons since the start of 2025. This unprecedented wave of mill shutdowns including major facilities operated by International Paper, Georgia-Pacific, and Smurfit Westrock, is being driven by sustained weakness in corrugated box demand, cost inflation, and global trade disruptions.
Despite this sharp contraction in supply, the market remains oversupplied in the short term, as box shipments have declined more than 10% since 2022. While current pricing remains relatively firm due to recent increases, the full impact of supply rationalization is yet to materialize.
While near-term demand remains soft, these closures are poised to tighten market supply by late 2026, potentially restoring pricing power to producers.
This article examines the key drivers behind recent closures, analyses demand and capacity dynamics, evaluates long-term price risks for buyers, and provides strategic considerations for procurement buyers amid a volatile and rapidly restructuring industry landscape.
Drop in US Box Shipments and Demand Contraction
The corrugated board industry’s correction is primarily demand-driven. Following a pandemic-era boom in e-commerce and packaging, US corrugated box demand has steadily declined.
US corrugated box demand has witnessed a significant downturn, declining by approximately 8% between 2022 and 2024. This marks a sharp reversal from the 5-6% surge seen during the COVID-19 lockdown period (2020-2021), when e-commerce and essential goods packaging fueled demand. In Q1 2025, box shipments registered a year-on-year decline of roughly 2%, bringing the cumulative drop in total shipments to over 10% since 2022. This represents the most pronounced contraction in box shipments since the Great Recession, when volumes plunged by around 12% during 2008-2009.
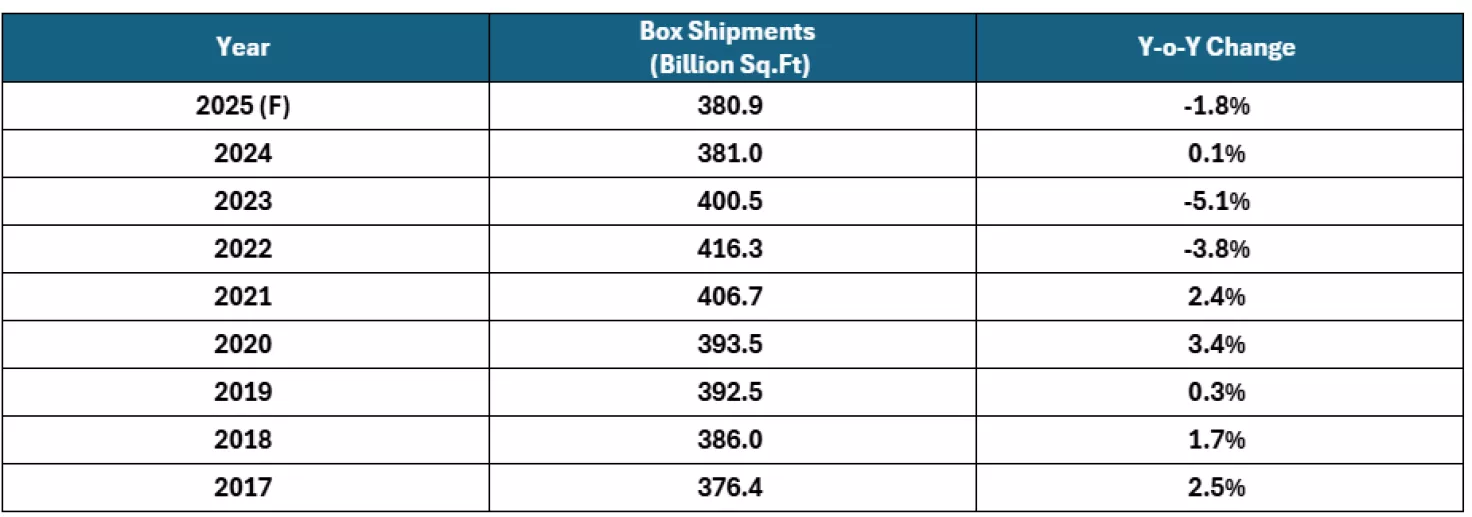
Key Drivers Behind the Decline in Corrugated Box Demand (2022–2025):
Post-Pandemic Inventory Normalization
During the COVID-19 pandemic, there was a sharp surge in e-commerce and home delivery, leading to increased demand for corrugated packaging. However, by late 2022, many retailers and
manufacturers began destocking the excess inventory accumulated during that period. This inventory correction significantly reduced packaging requirements across sectors.
E-Commerce Growth Deceleration
After the pandemic-driven boom, e-commerce growth has slowed and plateaued. While e-commerce is still an important demand driver for Corrugates, online retail is showing a slight deceleration in demand and no longer exhibits the significant growth rates seen in 2020-2021. As a result, corrugated packaging needs have declined proportionally, especially in non-essential categories like electronics, apparel, and household goods.
Macroeconomic Pressures
Slowing economic activity, persistent inflation, and rising interest rates have dampened consumer spending. The Trump administration’s tariff imposition has disrupted trade patterns, causing U.S. imports from China to drop around 60%. Additionally, industrial production slowed in 2023-2024, affecting bulk packaging demand in segments such as automotive, appliances, and furniture.
Sustainability Driven Packaging Optimization and Supply Chain Efficiencies
Many large buyers have aggressively pursued packaging optimization strategies to reduce material usage and improve environmental performance. This includes down-gauging/right-gauging the corrugated board grades, eliminating void-fill, and shifting to reusable or alternative packaging formats. These initiatives have led to reduced corrugated box consumption per unit shipped.
Many large retailers and logistics providers have invested in automation, robotics, and supply chain technologies to optimize order fulfilment. These advances have enabled more efficient packaging configurations, reducing the number of boxes used per shipment.
US Box Shipments Growth Rate Drops:
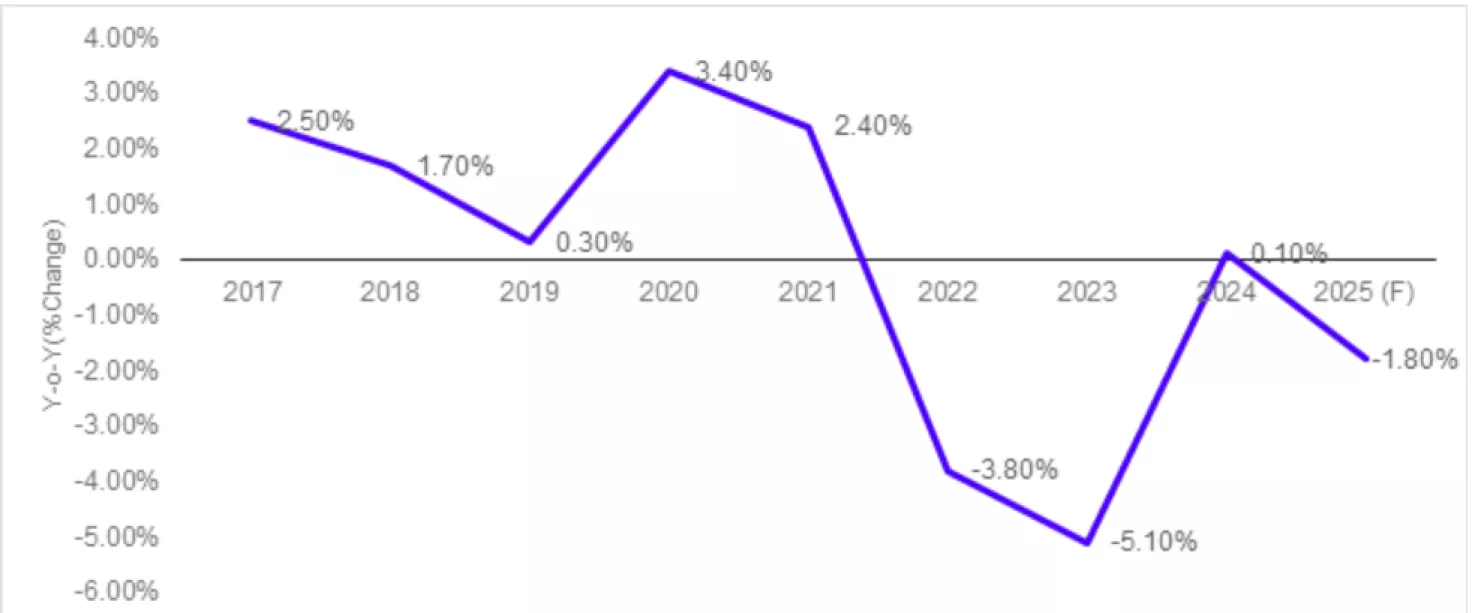
Large-Scale Capacity Closures in the US Corrugated Board Market:
In response to the persistent demand weakness, US Corrugated Board suppliers had initiated a wave of permanent mill closures to bring capacity in line with current consumption levels. Between early 2022 and mid-2025, around 3.5-4 million tons of board capacity had been shut down from the market.
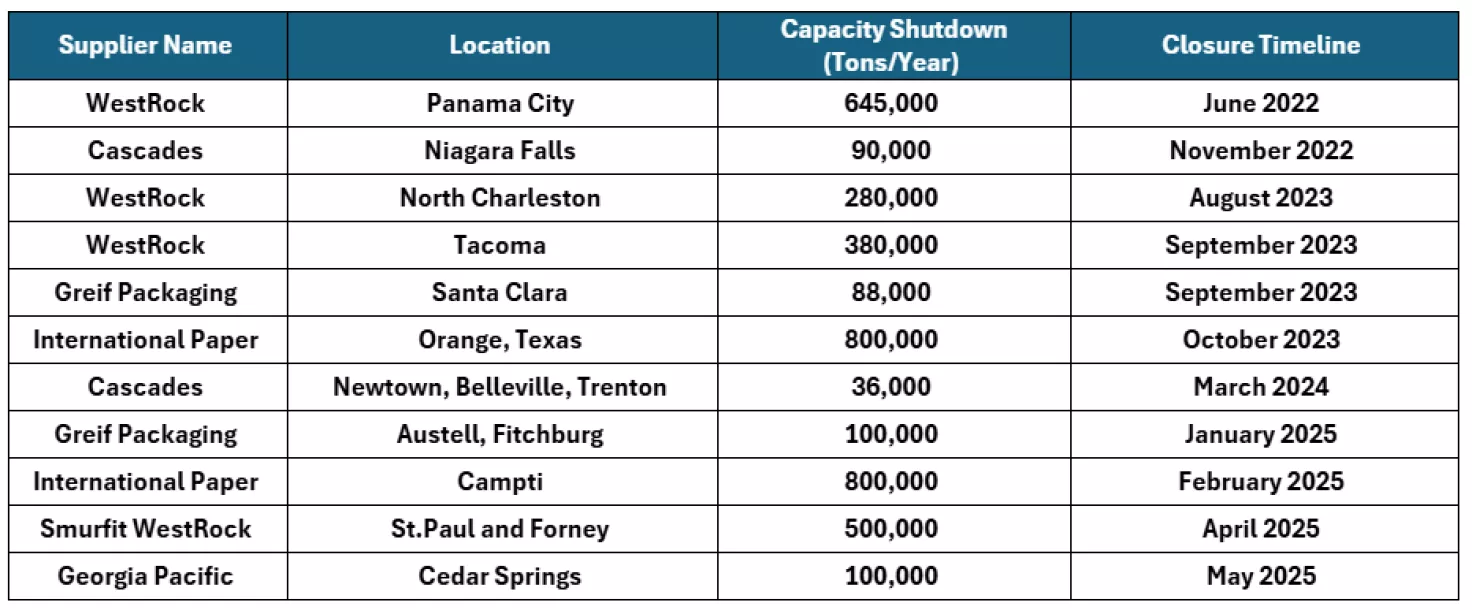
Total capacity closures across these mills is around 3.5-4 million tons and about 1.8-2 million tons of the 2025 closures are virgin corrugated board grades.
Major Drivers Behind the Capacity Closures
Demand-Supply Imbalance: With corrugated box shipments falling nearly 7-8% over the past two years, producers are aligning their production footprint with lower consumption levels to avoid oversupply. Mills ran below optimal operating rates dipping as low as 87% in 2023, eroding producer margins and pricing leverage.
Cost Optimization: Many of the closed mills are older, high-cost facilities with suboptimal scale, energy inefficiencies, or higher labor intensity. Shutdowns of high-cost virgin mills are helping reduce excess supply and improve margins for suppliers.
Focus on Integration and Margin Expansion: Suppliers are increasingly shifting focus toward higher-value, integrated operations, and expected to invest in automation and new state-of-the-art converting capacities.
Market Landscape post Capacity Closure
Despite the magnitude of closures, the majority of corrugated box makers remain unconcerned about immediate shortages. The primary reason is that current demand levels are insufficient to absorb the remaining capacity. US corrugated board operating rates averaged around 91% in 2024, down from an average of 95% in the 2014-2018 period.
Demand has not recovered sufficiently to justify price increases, even amid supply cuts as no significant seasonal uplift occurred in Q2 2025 and corrugated box buyers continue to delay new orders. Consequently, the market is witnessing minimal supply tightness. Buyers have prioritized managing existing inventories rather than locking in new volumes.
Implications of Capacity closures on the Supply Chain
Potential Reduction in Regional Supply Options: Closures in the Southern US, which is a key sourcing region, may lead to tighter supply and longer lead times around this region.
Supplier Consolidation Risk: With Smurfit Westrock and International Paper controlling larger market shares post-closures, negotiating leverage may shift toward suppliers in certain grades.
Shift in Product Mix: As older virgin mills close, some converters are adjusting to more recycled or blended alternatives, which may affect performance specifications.
Supply Tightness Post Pick-Up in Demand levels: These are permanent closures and will lead to supply tightness when demand rebounds around late 2026.
Price Implications: Despite ongoing capacity reductions, a significant price escalation in corrugated board is unlikely until late H1 2026, as soft demand conditions are expected to absorb the near-term impact of tightening supply. Prices are projected to remain relatively stable through early 2026, with upward pressure materializing only as demand begins to recover in late H1 2026, potentially resulting in price increases of approximately 3-4%.
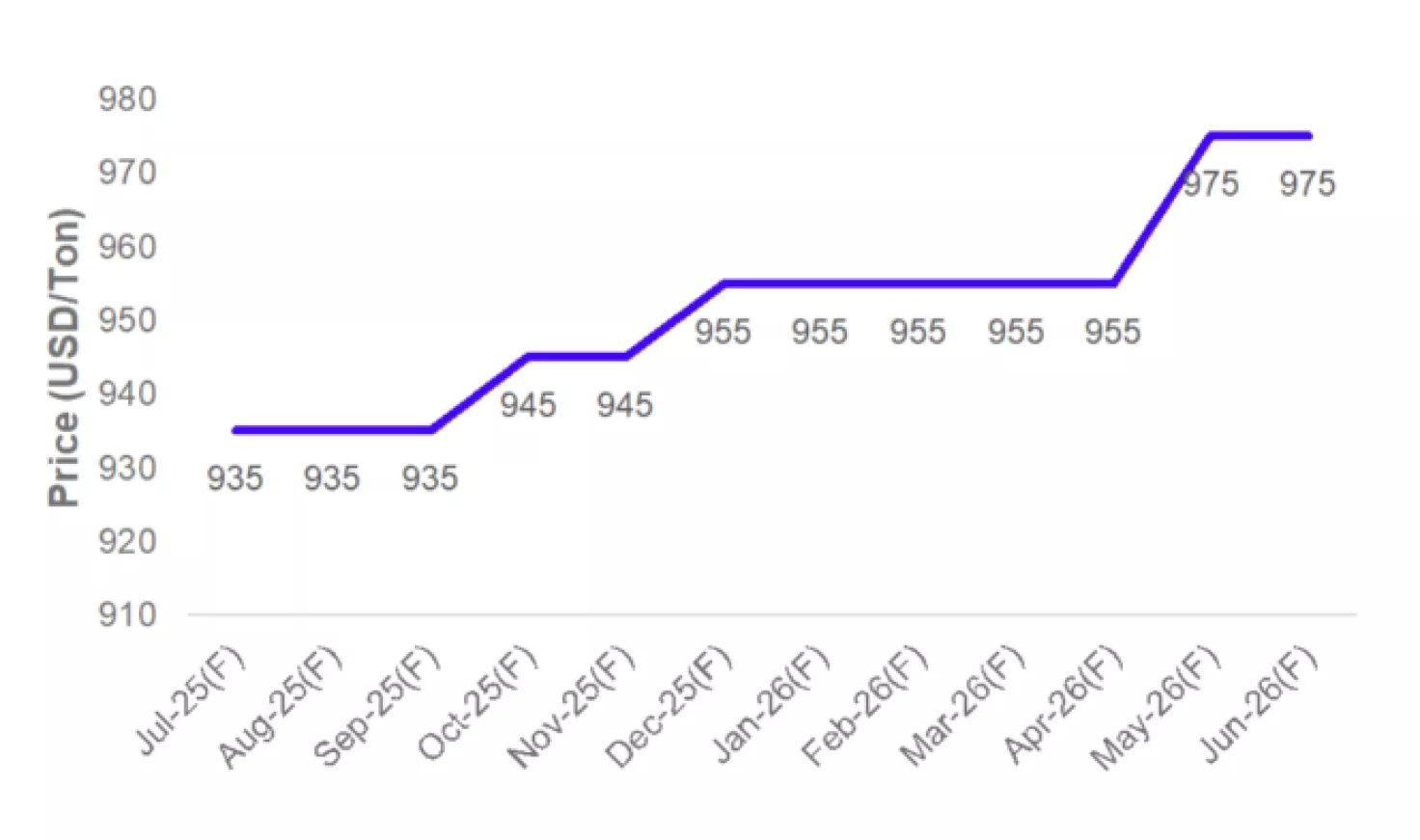
Strategic Recommendations for Buyers
The recent wave of corrugated board capacity closures, coupled with soft demand and geopolitical volatility, has altered the market landscape for procurement. While current pricing is muted due to weak box demand, supply contraction and ongoing capacity closures are expected to tighten the market by late 2025 or early 2026 when there is a rebound in demand levels. It is essential to build resilient sourcing strategies before market tightness translates into price inflation and supply constraints.
Diversify Virgin Fiber Grade Usage for Cost Optimization: The recent capacity closures have predominantly impacted virgin kraft linerboard, while recycled grades are expected to see fresh investments and increased availability in the near to medium term. Procurement teams are advised to collaborate closely with converters to transition toward high-performance recycled linerboard wherever technically viable.
Additionally, buyers should reassess current packaging specifications particularly in non-critical primary and secondary applications to identify opportunities for optimizing material inputs. Strategic blending of virgin and recycled content can help reduce costs and mitigate risks associated with constrained virgin supply.
Developing Strategic Supplier Relationships: As corrugated board capacity increasingly consolidates among a few dominant players, ensuring preferential access and favorable contracts becomes critical and buyers should proactively engage in joint demand forecasting and rolling volume commitments to position themselves as preferred customers.
Exploring volume-guaranteed contracts can unlock benefits such as fixed pricing, lead-time assurance, and priority allocation during tight supply periods. Additionally, partnering with suppliers that offer digital transparency into mill lead times will enhance supply chain visibility.
Monitor Market Developments: Mill operating rates are projected to trend upward, potentially reaching the critical 95% threshold by the second half of 2026, driven by an anticipated rebound in demand. Historically, operating rates at or above this level have been closely correlated with upward pricing movements. As such, procurement teams should closely monitor the market for potential price increase announcements from major producers, particularly following Q2 2026.
Buyers must monitor capacity developments and price hike announcements; track operating rates and mill downtime, closures, and restarts across key suppliers; and monitor Pulp and OCC costs to stay informed on the market trends.
Conclusion
The US corrugated board market is expected to enter a tighter supply dynamic following an unprecedented round of mill closures. While the near-term oversupply has kept prices from surging, buyers should prepare for potential price volatility in H2 2026 and beyond. As suppliers shift towards a more consolidated, efficient, and cost-driven model, supply chain agility, data-driven planning, and proactive supplier engagement will be essential tools for navigating the changing landscape.
A strategic, forward-looking procurement approach will enable buyers to lock in reliable, cost-effective supply in a projected tightening of supply in the long term.
Request a demo
Discover how our solutions can benefit you. Partner with us to unlock potential and drive success. Let's work together to achieve outstanding results.
Get in touch
We’re here to assist you! If you have any questions or need support, don’t hesitate to reach out. Contact us today and we’ll respond promptly to help with your needs.